Profile of a Large-Scale Mobile Layer Shelter by Mike Badger
- The Egg Carton Store
- Jun 10, 2019
- 3 min read
This article was republished, with permission, from APPPA Grit Issue 96. Mike Badger is the Executive Director of APPPA and host of the Pastured Poultry Talk podcast.
Other members have written about the large-scale, daily move broiler shelters that can hold up to 600 broilers at one-time. And I’ve heard stories from the field of people building $50,000 egg mobiles—luxurious proof of concepts but not practical. Then Cliff Stoltzfoos of Stoltzfoos Layers in Kinzers, Pennsylvania, caught my attention with his mobile shelter for layers. He has some of the same efficiency improvements you might expect to find in a larger-scale commercial operation, but his shelters are moved through the pasture every day.
I thought it would be reasonable to share and profile one of the most innovative egg mobiles I’ve seen on pasture.

Daily Move with Small Equipment
Stoltzfoos Layers manages 4,000 layers on pasture in batches of 650 birds. Each day, the shelter is moved ahead by 100 feet. The 100 feet, according to Cliff, is the distance required to get the birds into fresh pasture for the day’s foraging; this allows the hens to graze in front and back of the shelter on fresh pasture.
His early pasture shelters were constructed of wood and would flip over in the high wind storms, which causes a host of problems, including death, destruction, and dropped hen productivity. The shelters evolved to a hoop house or green house design on a custom fabricated trailer frame that’s low to the ground. The design includes a tandem axle in the rear, and has a footprint of 12’x25’. The result is something that is stable and easily moved with a side-by-side vehicle, such as a Gator.
Solar Powered
Supplemental lighting evens out the egg production throughout the year. And on pasture, the most efficient way to do that is with solar, which is where Cliff’s design ultimately ended up. Before solar, he tried to use a 1,000 watt generator to power the lights. This worked until somebody forgets to start the generator or it runs out of gas or experiences other problems.
In the current design, the solar panel charges a battery bank that not only powers the lights, but it also powers the automated feed augers and the nest box timers.
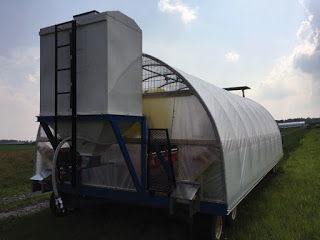
Clean Eggs
Nest boxes open and close on timers, which is Cliff’s way of preventing hens from lounging in the nest boxes. Add in roll out nests boxes, and the eggs stay clean, which was his solution to dirty floor eggs in previous designs. By keeping the eggs clean, Cliff can sell unwashed eggs to his many customers who demand them. As an aside, many APPPA members have been able to keep eggs clean and hens from lounging in the nest by using curtains in front of the nests.
When the eggs roll out of the nests, they land on a conveyor belt. When collecting eggs, a person can stand on the outside of the shelter and hand crank the eggs from inside the shelter to the egg collecting station. The person collecting eggs can pack them directly into cartons or flats.

Feed and Water
Each shelter has a one-ton feed bin attached to the rear of the shelter that feeds an automated feeding system. A sensor detects when the feed drops below a set point and automatically delivers more feed to the feeders.
On pasture there are a lot of humidity changes which can cause problems for the switching systems found on automated feeding systems. There are no moving parts in the sensor system, reducing the chance of a sensor failure.
Each shelter has a 150 gallon water tank inside that gravity feeds a nipple line. It can be filled through a fill line. Cliff uses a 500 gallon tanker to deliver water in the field, capable of filling a tank in less than 40 seconds.
The payoff
Cliff’s egg production is currently averaged out at 80% from the time he gets his ready-to-lay pullets. That’s up from the roughly 50% yearly average he started from. He attributes the efficiencies in shelter design to the improvement in management.
댓글